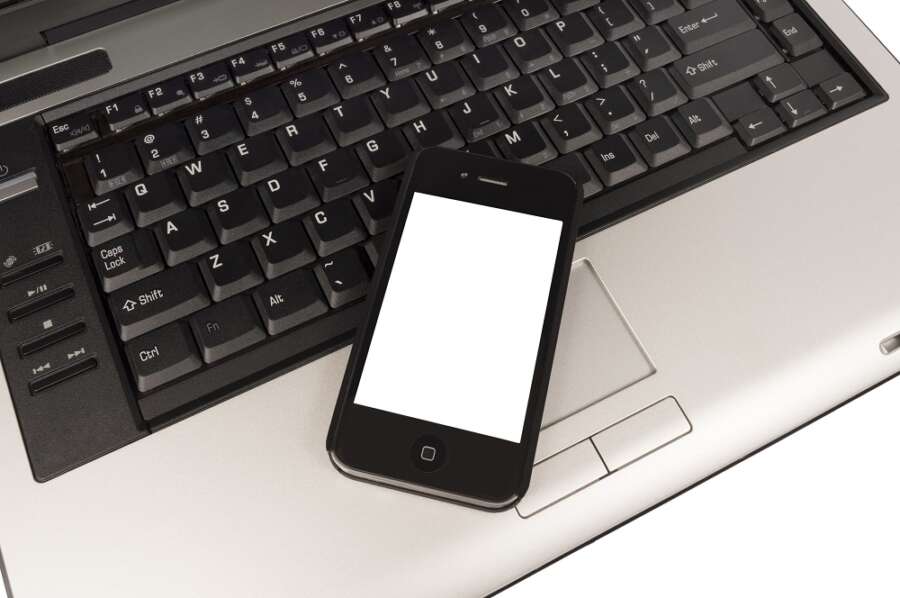
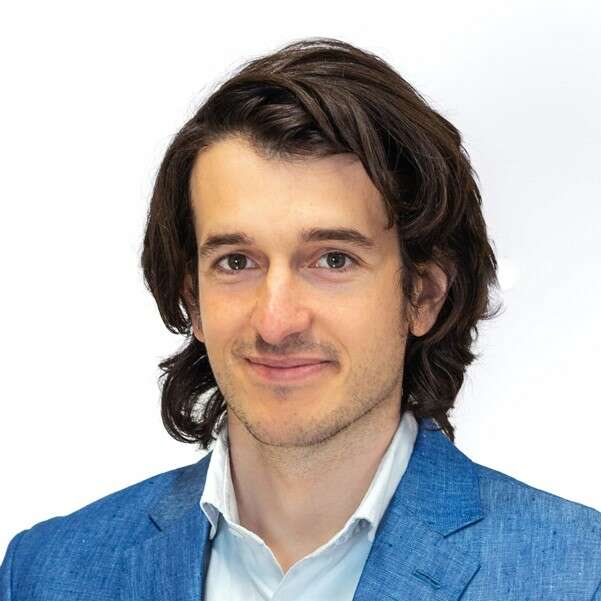
There is a real cost when it comes to the value of human labour in the logistics industry. An over-reliance on this labour has always been a constant, recently exacerbated by the global pandemic, and exposed in geopolitical events such as Brexit, which saw a large proportion of the UK cheap labour workforce swiftly felled with one sharp blow. Automation is overcoming the need for cheap labour in some areas of the supply chain – particularly in warehousing and transportation – but its impact goes far beyond the popular misconception of robots picking and packing items in a depot.
We’re seeing teams across operations, warehousing and customer service spend time on managing data and using digital tools to drive automation across the full spectrum of logistics orchestration. This move away from using manual processes to manage systems and data is the key to unlocking greater overall supply chain value, by an order of magnitude. We’ve seen even less skilled workers (or “cheap labour”) able to make this transition. Rather than replacing jobs, technology is enabling the workforce that run these processes to work smarter and increase performance without adding headcount or CapEx.
Logistics resilience is achieved by not only deploying this automation, but also creating a more transparent working environment in which confusion over supply chain value is simplified. The end goal is to enable clients with the ability to automatically switch to carriers (so they can benefit from the best rate and performance on every shipment, a huge benefit in times of uncertainty and change).
Take ‘Black Swan’ events such as the recent pandemic; while a one-off event, the fallout from COVID-19 was seismic and the logistics industry was hit very hard by the restrictions on both passenger and freight air traffic. In fact, the vast majority of commercial air traffic is passenger traffic; around 50 percent of airfreight is carried on passenger flights. So when passenger flights came dramatically to a halt in the first few months of 2020, freight charges rose sharply. In the scramble that resulted from reduced airfreight capacity, freight forwarders, large corporates and express transporters were competing for space. This resulted in raised costs that were passed on to customers.
Often these additional COVID costs have been baked into freight charges and will have been invisible to the staff responsible for reviewing supplier invoices. Even if a business has a contract for preferential rates with a logistics carrier, it is still exposed to these additional costs, and has little or no contractual control over when surcharges will occur. For example, in relation to COVID surcharges, UPS simply noted: ‘Surcharges are subject to change without notice and peak periods may be extended or otherwise changed’. In fact, 7bridges observed a variance of up to 100% in surcharges during April-June 2020 across the top logistics providers.
The businesses that have already deployed automation technologies have weathered the blows dealt by events such as the COVID pandemic and Brexit better than others. We’ve seen our own customers rapidly adapt to things like border closures and the DPD road service cancellation at the start of the year thanks to the automation of processes such as logistics carrier selection. While some businesses were unable to fulfil orders, they were able to change routes and logistics carrier in near real-time, avoiding disruption.
The current lorry-driver shortage is another shortcoming in human labour that can be mitigated by automation. Businesses are on high alert for continued disruption in their supply chains, as Black Friday and Christmas shopping peaks loom and, while there isn’t a magic solution to create more drivers, there are solutions to minimise the risk of delays to shipments. Businesses using Artificial Intelligence (AI) to dynamically select their logistics carriers are able to fulfil orders without delays, as the AI technology uses a combination of real-time and historical performance data sources to calculate the most reliable supplier for each job.
At 7bridges, we’ve seen this ‘multi-carrier’ logistics strategy successfully see our customers through all of the supply chain crises of the past 18 months. It’s also helped our customers save on average, 30% on their direct costs, as our AI is able to model the best outcome for every order based on delivery time, price, and customer preference. It’s actually empowering this type of employee to work smarter, so they can help optimise their supply chains while again reducing costs and without increasing headcount.
Automation in the workplace should therefore not be seen as a direct threat to human labour, rather an agile system which, while running in the background, augments workplace management and allows businesses to create logistics resilience and fully realise supply chain value.