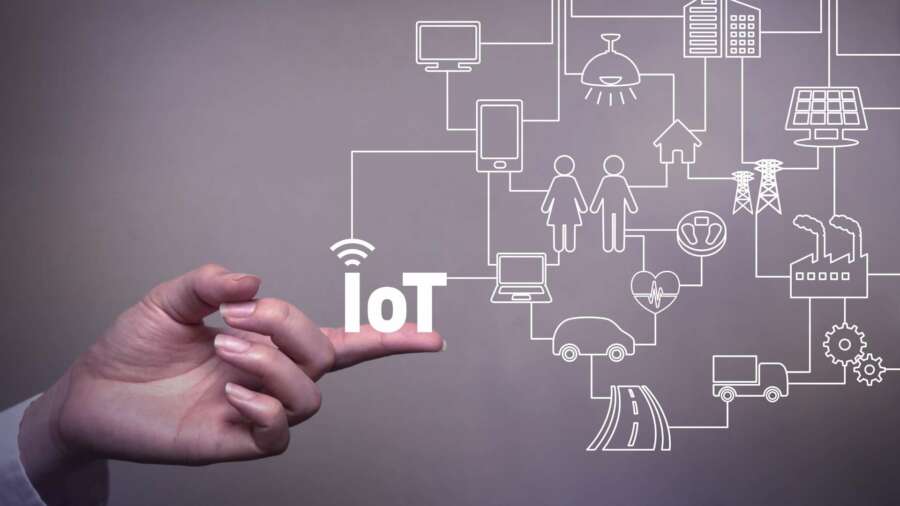
Lukas Baur, Executive Vice President Strategic Solution Sales, TeamViewer
The Internet of Things (IoT) has become fundamental to business growth. In fact, McKinsey recently revealed that the amount of businesses using IoT grew 12 percent from 2014 to 2019. This is only set to continue, with GSMA predicting that IoT will grow to a $1.1 trillion industry by 2025. IoT has been, and will remain, crucial to developments such as the rise of Industry 4.0 as remote working and increasingly complex machinery require further monitoring and support than is currently undertaken. As it becomes ever more fundamental to businesses growing their digital offerings, so will predictive maintenance. It is a combination of remote monitoring and data analytics, that is key to managing and sustaining the technology that underpins our digital world.
But what challenges are businesses facing with IoT, and why is predictive maintenance the solution? The simple answer is preventing downtime. In the manufacturing industry alone, for example, downtime is estimated to be costing businesses more than $50 billion each year, according to Deloitte. It is therefore crucial that when utilising IoT and embracing digital transformation, leaders use the latest solutions such as predictive maintenance tools to monitor and mitigate the impact of downtime.
Fundamentally, predictive maintenance enhances smarter remote monitoring and the maintenance of systems, empowering operators with the data they need to run at optimum levels and take preventative measures against downtime. It’s time for businesses to embrace predictive maintenance, overhaul outdated, risk inducing systems and realise the real benefits of IoT. Here’s how to do so:
Look into the future with predictive maintenance
Existing maintenance models, either reactive or preventative, still rely on largely manual processes as the data on how machines are functioning remains unconnected. This means that companies are struggling to respond quickly to mitigate failures. As over one million IoT devices are expected to go into operation every hour in 2021, predicted by Gartner, businesses must do everything they can to maximise uptime, maintain productivity and keep their customers happy. Those still relying on outdated, fragmented infrastructure run the risk of falling behind their competitors, and losing customer demand.
This is where predictive maintenance comes in. It relies on connecting machines and live streaming data on how those machines are operating with predictive algorithms. In a setting such as a smart city for example, constant monitoring of IT connectivity is crucial to ensure all aspects of the city are running smoothly, from waste management to traffic cameras, street lamps and CCTV. Predictive maintenance, therefore, allows systems and machines to be monitored and maintained before issues occur. In turn, removing the need for someone to be physically onsite running checks.
To see the best possible results of predictive maintenance, businesses must focus on implementing it into all aspects of the workflow. Achieving this means leaders can save valuable employee time through the use of automation, view all processes holistically, and reduce on-site maintenance costs. In turn, downtime will no longer be one of the biggest challenges facing businesses, but a manageable issue that can be controlled by predictive maintenance.
The benefits of being connected
So, how can leaders maximise the benefits of predictive maintenance? They can follow these four easy steps:
- Connect IoT sensors to all infrastructure used in the workflow. This will enable data streaming from legacy or embedded equipment and unlock real-time monitoring of their operating status. In turn, the business can better predict a machine’s performance over any period of time, ensuring it has a holistic view of its IoT estate and put the measures in place to prevent downtime.
- Predict outcomes using predictive analytics from the legacy equipment data. These diagnostics will highlight any anomalies or faults and provide you with a full assessment of the state of the equipment, and an understanding of how to troubleshoot failures.
- Automate processes. Predictive automation can identify the best methods to optimise existing processes, and advise the best person to resolve any issues. One example of automated optimisation is the classification of potential failures. This means work orders can be sent directly to engineers or technicians rather than them needing to queue and wait to be allocated tasks manually. This will save resources, reduce downtime and boost productivity.
- Support and fix your machines using remote capabilities or Augmented Reality (AR). An example of this would be utilising AR tools to remotely assist and guide operators through maintenance workflows. This ensures accuracy and speed when fixing infrastructure, and builds confidence among operators and support technicians as predictive alerts give them sufficient time to plan for any downtime.
The benefits from these steps are clear: around the clock monitoring with predictive analytics can be used to understand and create maintenance and performance forecasts. This test of predictive maintenance is key for operators to unlock the secret to running at optimum levels and taking preventative measures against downtime.
Real-time rewards
As issues are detected, technicians can immediately access infrastructure or machines remotely to adjust configurations, trigger restarts, or change settings to troubleshoot problems. But this isn’t all. As a result of putting predictive maintenance in place, technicians can be more productive at work. They can use the data to predict and prevent failures, rather than maintaining on a reactive basis, and the entire business can run at a higher capacity.
The growth of IoT and Industry 4.0, and the sudden impact of the pandemic has meant that companies must act now to implement the technologies that they have always planned to adopt. To optimise workflows, minimise downtime and thrive in the wake of the global pandemic, predictive maintenance is the place to start.