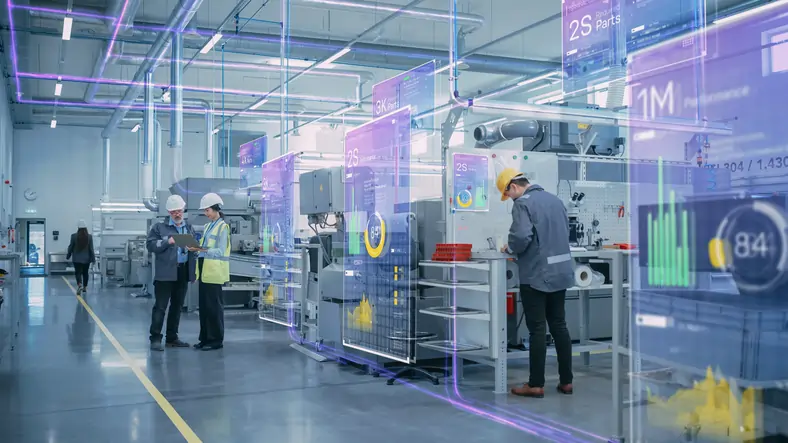
The future success of the manufacturing sector is now dependent on digital empowerment from physical systems to IT process to people, to provide the increased visibility and flexibility required to improve manufacturing efficiencies and decrease costs. This means leveraging data from the shop floor to the c-suite. Step forward the in-demand smart factory. Adoption rates are on the rise and so too is the global smart factory market size, which is expected to grow from $129.74 billion in 2022 to $321.98 billion by 2032, with a CAGR of 9.525.
There are three areas manufacturers need to focus on to go smart, says Kevin Bull, Product Strategy Director at Columbus UK, – data-driven insights, automated demand forecasting, and an effective customer experience and engagement strategy – all of which can be achieved with a new business customer experience mindset and smart technologies.
Smart factoriesas defined by Gartner are a ‘concept used to describe the application of different combinations of modern digital technologies to create a hyperflexible, self-adapting manufacturing capability. Smart factories are an opportunity to create new forms of efficiency and flexibility by connecting different processes, information streams, and stakeholders (frontline workers, planners, etc.) in a streamlined fashion.’
So, what is required for manufacturers to make the smart move?
A key component of a smart factory set up is digital transformation and Industry 4.0 technologies including IoT sensors, ERP, AI, and cobots – all of which will help improve manufacturing efficiency. However digital transformation technologies are constantly changing, and the manufacturing industry is under pressure to keep up. But are they ready? All signs say yes, with a recent report finding that over the next 12-24 months, over 60% of manufacturers are focusing on improving their manufacturing agility and this is where smart factories can help.
Automation is already a common practice for many manufacturers, but smart factories take it to the next level and operate automatically. By being more adaptable because of their ability to embrace new technology, smart factories can change in real time. Thus, linking every component of the value chain together to allow for manufacturing decisions to be made precisely and quickly.
There are three key components to creating a smart factory which are all underpinned by cutting edge technologies and they are: data-driven insights, automated demand forecasting, and an effective customer experience and engagement strategy.
Unlock growth opportunities and deliver a personalised experience by integrating smart systems
Smart manufacturing is all about delivering the right information to the right people at the right time. A manufacturer’s journey relies on trusted data-driven insights but data management remains one of the biggest time sinks in any organisations, especially when manufacturers rely on legacy systems that can’t effectively integrate with other businesses systems to share data.
The accurate and automatic flow of data between systems is crucial to increasing efficiency and production. This means it’s essential to have a seamless horizontal integration between operational systems and vertical integration through connected manufacturing systems, as well as end-to-end, holistic integration through the entire value chain.
The first stage of unlocking the data goldmine is to analyse the business processes that are causing the most pain, and then to analyse the data that flows through them to identify areas of inaccuracy, duplication, and incompleteness. From here, manufacturers can begin to build a data strategy that reduces waste and optimisesthe data value stream with smart manufacturing technologies.
Modern data collecting and analytics tools that integrate with each other can be effective in maximising productivity. Take the example of integrating a CRM and ERP system – together these smart systems can eliminate data siloes, minimise manual work, and provide manufacturers with a 360-degree view of customer buying habits, order history, and preferences. This will help manufacturers deliver more personalised experiences and track changes in customer behaviour to determine opportunities for future growth.
Gain actionable collective data quickly by switching from a reactive operating model to a proactive and predictive one
The most effective way manufacturers can operate more efficiently, increase production, and increase margin is to shift from a reactive operating model to a proactive,predictiveone that leverages collective data. Actionable insights from AI, machine learning, and IoT outputs provide a connected digital feedback loop which enables real-time operational optimisation. This ensures organisationshave the ability to proactively leverage this new-found knowledge across the entire value chain.
Demand forecasting isused to anticipate demand with enough time to manufacture the right amount but often the problem is capacity, demand, and cost aren’t always known parameters. Variations in demand, supplies, transportation, and lead times create uncertainties which can have widespread effects on production scheduling, inventory planning, and transportation – and this is where machine learning tools can helpmanufacturers produce the exact amount of product to meet demand. No more. No less.
Accurate demand forecasting with machine learning tools tries to predict future demand for a product or service in a supply chain by relying on economic and consumer conditions in the marketplace. Demand forecasting looks at historical data, market trends, missed sales, economic conditions, competitors’ actions, and a variety of other factors to anticipate future customer behaviour. It’s the first step in production planning and a key requirementto addressing uncertainties in supply chains.
Manufacturers can use these insights tomake more informed decisions about production, inventory, and staffing – avoiding shortages or overages, which can be costly and damaging to the business. Accuracy in forecasting significantly reduces operating costs and makes businesses more efficient, more profitable, and better equipped to deal with periods of unpredictable uncertainty.
Value-added CX is a company effort – from the top to the bottom
A connected supply chain is not truly effective if the connectivity ends with the product.
Digital customers are now more connected and empowered than ever before. With so many options available at their fingertips, customers won’t hesitate to take their business elsewhere if they feel their needs aren’t being met. Unsurprisingly, research found that 63.73% of manufacturers placed creating a seamless customer experience as a top business priority.
It’s up to manufacturers to rethink customer experience and engagement (CXE) approaches – so what smart manufacturing tools can help meet this pressure?
Digital technologies such as a customer relationship management (CRM) system can help manufacturers not only deliver high quality products but also provide exceptional customer experience to meet the higher expectations of the new age customer – but the technology advantage doesn’t stop there.
Manufacturers must meet their customers where they are and that’s online!
As with other industries such as retail, the buyer’s journey has moved online and it’s up to manufacturers to meet customers where they are and add value through content and personalised experiences, with all digital experiences offering high quality interactions. Manufacturers don’t need to digitise the whole customer experience – simply digitising product catalogues can be a step towards improving customer experience. Essentially, it’s about giving customers more autonomy such as allowing them to view accurate stock levels, configure product functionalities, and customise pricing.
Due to the ever-lowering price of IoT sensors, state-of-the-art mobile devices, and cloud-based statistics aggregation, manufacturers can enhance service standards and margins by means of providing remote tracking and proactive maintenance that complement damage/restoration assist.
A new smart look for manufacturing
Traditional factories simply can’t keep up with the level of efficiency, accuracy, and flexibility that smart factories operate at due to their effective use of cutting-edge technologies across entire manufacturing operations.
The future is looking bright for the manufacturing industry with the right digital tools and a refreshed customer experience mindset, the new era will be dominated by connectivity, autonomy, and visibility. Smart factories are primed to take manufacturers to new levels of efficiency and productivity!